Необычные РВД для японских автовышек
Первая японская автовышка появилась в нашей организации в 2005 году. Тогда это была первая японская автовышка не только у нас, но и в городе. Это была автовышка с высотой подъема 13 метров. Она очень быстро завоевала популярность за счет своих небольших габаритов, маневренности, высокой скорости работы, точности позиционирования. Да и выглядела она тогда, по сравнению с отечественными автомобилями, намного привлекательнее. Если с маслами и другими техническими жидкостями проблем небыло - рынок был насыщен данными товарами, то с запчастями и ремонтами возникали сложности. Да, поломки были, но в основном все сводилось к мелочам. То резинки, то шаровые, то где-то подварить. Пару лет особых сложностей не возникало. Запчасти можно было купить на разборках, они еще ходили потом довольно долго. Но с гидравликой возникали сложности. Элементы этой части машины стоили очень дорого и найти их было сложно. Так, гидравлический насос в оригинале даже сейчас стоит нерезонно дорого. Приходилось что-то мудрить от наших машин, переделывать, перетачивать, ставить переходники. Прошел какой-то период и износились рукава высокого давления внутри стрелы. Пришло время их менять. Сервисов, которые могли тогда сделать такую работу, просто небыло. Японская спецтехника была никем не изучена и никто не взялся за эту работу. Пришлось осваивать все самим, учиться на собственных ошибках.
Первый раз разборка стрелы заняла 5 дней. Мы даже не знали с какой стороны подойти к стреле. Пришлось разбирать все до винтика. В тот ремонт было много сделано лишнего, но без этого невозможно было получить опыт. А опыт, полученный на ошибках - самый лучший. Но проблема оказалась не столько в разборе стрелы, сколько в РВД, которые были внутри нее. Когда мы сняли шланги, встал вопрос, чтобы изготовить новые. Уже по виду было понятно, что это необычные рукава, а фитинги вообще были с дюймовой резьбой. Поездив по городу по изготовителям РВД стало понятно, что ничего мы тут не найдем. Мало того, что на нас смотрели как на сумашедших, так еще поступали бредовые предложения об изготовлении всевозможных переходников с дюймовой резьбы на отечественную метрическую. Благо тогда хватило ума не поддаваться на эти бредни и не останавливать поиски. Естественно в своем городе мы ничего не нашли. Одна единственная японская автовышка на весь город - информации и специалистов никаких небыло. Благо столица была недалеко - на нее и оставалась вся надежда.
Посетив в столице специализированный центр по изготовлению рукавов высокого давления, мы получили информацию, что такие рукава можно изготовить по образцам, и проблем с дюймовой резьбой и фитингами небыло. Воодушевившись надеждой на светлое будущее, мы взяли в охапку наши старые шланги, запаслись большой суммой денег и отправились в столицу делать новые рукава высокого давления по нашим образцам. Процесс изготовления занял несколько часов. В конечном итоге мы получили новые рукава из морозостойкой резины с одинарным металлическим армированием. При этом наружные диаметры рукавов были незначительно больше оригинала. По словам мастера, это небыло проблемой, типа 1 мм роли не играет. А ключевое слово "морозостойкая" вообще внушало большие перспективы на будущее. Как хвалился мастер, который изготавливал рукава: "В Японии таких морозов, как у нас, не бывает", так что эти рукава должны были служить вечно. Но на тот момент мы вообще не понимали ничего и верили всякому бреду, главное, что проблема была решена.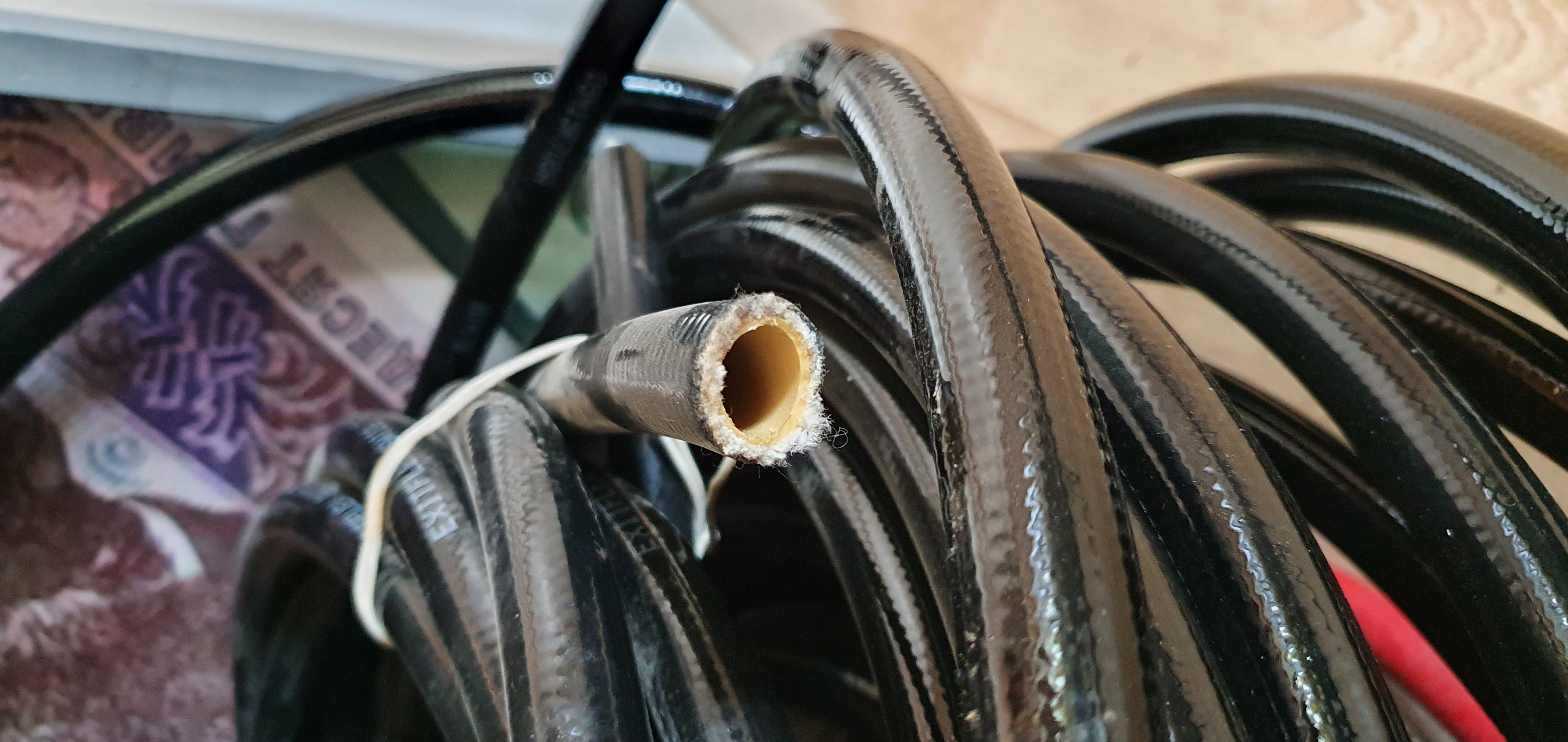
Новые рукава устанавливали еще неделю. Сначала не могли понять, какой рукав куда идет, потом переделывали натяжные троса, под них вытачивали новые натяжители с резьбой. Все это запасовали на ролики. Потом на роликах меняли подшипники, вычищали из стрелы грязь и ветки. Какие-то пальцы вытачивали, совещались про натяжку шлангов и т.п. - в общем неделя рабочего процесса. После установки и сборки вздохнули - гидравлика заработала. Стрела выдвигалась и задвигалась. Это была победа. Мы, парни из русской глубинки, встали в один ряд с инженерами из Японии, смогли починить ихнюю технику своими собственными руками. Эйфория одним словом.
Правда радость оказалась недолгой. Не прошло и месяца как шланги внутри стрелы потекли снова. Разбирая стрелу мы не могли понять, что же сделали не так. На этот раз разборка заняла уже два дня. Опыт уже был. Схема отработана. После разборки мы увидели следующую картину: шланги были все как-будто порезаны, проволока от металлического армирования торчала то тут то там. Создавалось впечатление, что шлангам не месяц, а несколько лет. На ум приходило несколько ошибок, которые мы могли допустить: неверная натяжка, попадание посторонних предметов внутрь стрелы, несоответствие посадочного места на ролике диаметру шланга, низкое качество шлангов. Но все предположения оказались неверными. Мы стали обзванивать другие фирмы в столице, чтобы собрать хоть какую-то информацию. И в одном представительстве чешкой фирмы, которая продавала различные шланги для производств, нам открыли в прямом смысле этого слова "новый мир" касательно наших рукавов высокого давления. Там пояснили, что уже сталкивались с такой проблемой и не раз ее решали. Предложили приехать к ним с образцами старых и новых рукавов, что мы незамедлительно и сделали. Приехав на эту фирму, мы ни разу не пожалели, люди в доступной форме, используя подручный инструмент показали нам что происходит с нашими рукавами и с теми, что мы заказали в другом месте, при движении по роликам, какие напряжения происходят внутри и почему у нас возникла проблема. Показали технические характеристики наших и "новых" рукавов. Оказалось, что сделанные рукава не соответствуют параметрам роликов, они не могут гнуться по такому маленькому диаметру, а металлическое армирование вообще не имеет гибкости и при движении по роликам просто рвет защитную оболочку и вылезает наружу. Более того наши рукава имели снаружи стойкое к истиранию покрытие, которое предназначено именно для движения по роликам и не стирается даже спустя продолжительное время. Разрезав наш шланг, они показали, что внутри имеется полимерная трубка, которая непосредственно держит давление и очень хорошо гнется, а армирует трубку синтетическое тканевое волокно, которое также имеет значительную гибкость без деформации. Выводом стало то, что резиновые рукава, даже с температуростойкой резиной, и уж тем более с металлическим армированием никак не подходят в нашем случае. После такой лекции пришлось идти за литром водки и закуской, чтобы как-то отблагодарить ребят из этой фирмы. Полученная информация на тот момент был очень ценной.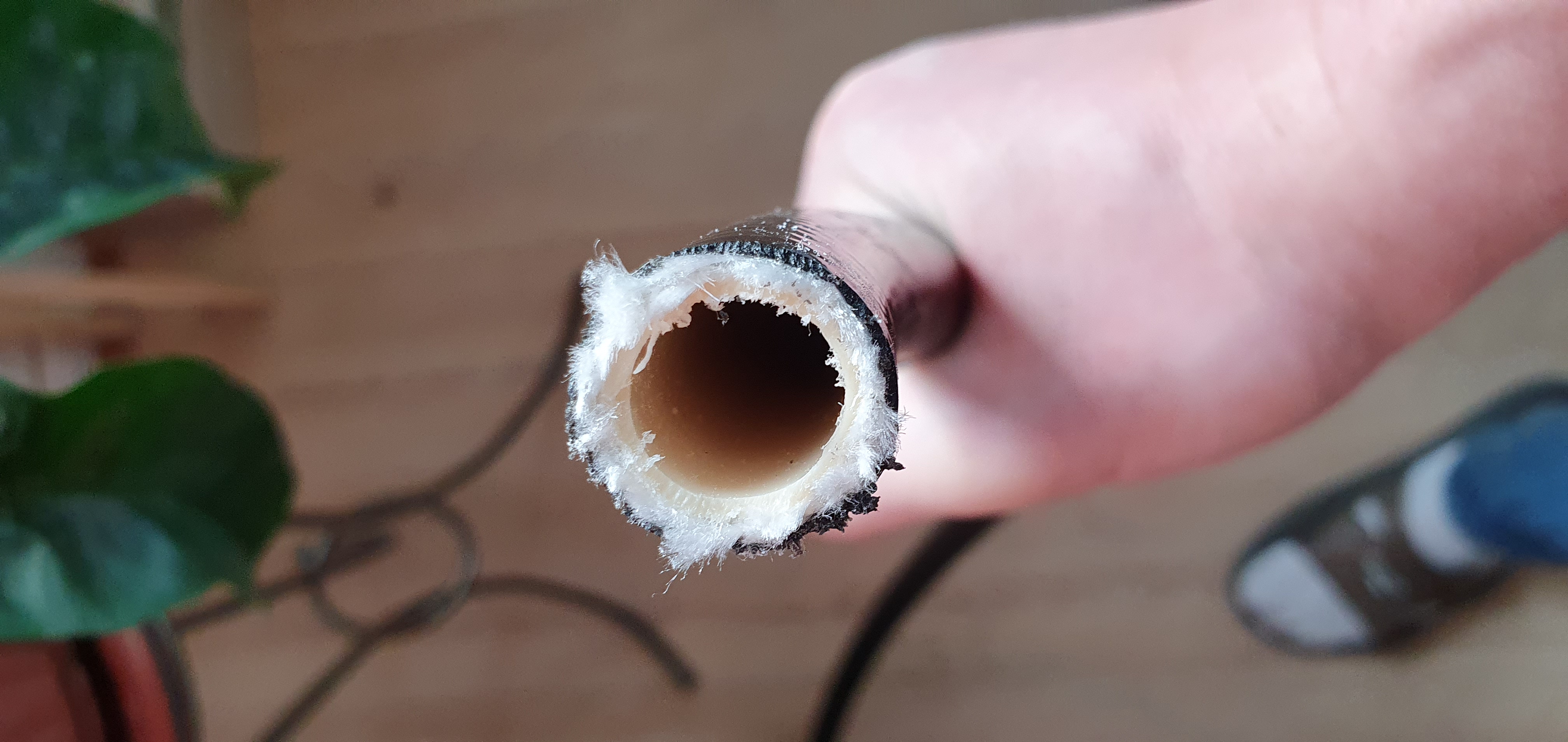
После небольшого перерыва удалось получить дополнительную информацию о том, что у них есть в продаже такие рукава и даже могут сделать опрессовку. Однако возникла проблема в том, что нет фитингов с дюймовой резьбой, поскольку такие не применяются в Европе. Однако осмотрев шланги, которые нам сделали в другой фирме, было предложено попробовать срезать с них фитинги и опрессовать заново. Все-таки литр водки и хорошая закуска наверно сыграли свою роль, а может ребята просто над нами сжалились, потому что в попытках решения этого вопроса дело уже доходило до слез. После просчета стоимости услуг и материала мы начали подбивать свои финансы, ценник оказался значительно дороже, чем отечественные шланги, но выхода уже небыло, цель была совсем близко. Денег немного не хватало, но нам сделали скидку на перспективу, что тоже было немаловажным фактором. В общем все эти разговоры, лекции и сама работа заняли почти полный рабочий день. Мы постарались помочь, чем смогли. Где-то поддержать, где-то отрезать болгаркой, что-то отмерить, в общем включились тоже в работу. Ну и скидку надо было как-то отрабатывать. По итогам дня мы получили в собственность термопластиковые рукава для нашей автовышки, при этом они были чешского (импортного) производства. Также получили рекомендации по натяжке и эксплуатации. Ну и вообще, все заданные вопросы имели ответ, что очень порадовало. Общение вышло очень продуктивным и душевным. А информация о том, что через несколько дней шланги надо будет подтянуть, поскольку они немного растянутся после того как были намотаны на бобину, вообще осталась с нами как должная аксиома, которой мы пользуемся и по сей день.
В результате данные шланги были установлены нами на автовышку. Через неделю была проведена их подтяжка. Отслужили они нам верой и правдой почти 7 лет - вот что значит качество. А встреча с этими ребятами для меня осталась в памяти до сих пор. Может времена тогда такие были, может люди просто отзывчивые попались. Сейчас уже все реже встречаешь такое, люди стали другими, за копейку "давятся", чего уж говорить про отношение, если не "послали" и то хорошо. Рукава такие, слава прогрессу, появились, по крайней мере в больших городах, в свободной продаже. Ну а мы, чтобы не рисковать и не тратить время на их поиски, купили обжимное оборудование, завезли эти рукава к себе на склад. Отработали технологию и теперь можем предложить услуги по изготовлению РВД на японские автовышки. Получается вроде неплохо, есть клиенты даже из ближнего зарубежья. Многие машины ходят уже больше 5 лет. Ну и ремонт той первой автовышки перерос у нас в полноценный сервис по гидравлике. Разбираем стрелы теперь за день, перебираем гидроцилиндры, переделываем насосы - на своих машинах научились...
© Дядя Fedor, февраль 2021 г.
При перепечатке материала прямая ссылка на сайт www.podnimai.ru обязательна!
Смотрите видео про экскаватор-погрузчик на моем канале в Яндекс.Дзене
Читайте еще статьи на нашем сайте:
- про японскую автовышку
- про автокраны
Первый раз разборка стрелы заняла 5 дней. Мы даже не знали с какой стороны подойти к стреле. Пришлось разбирать все до винтика. В тот ремонт было много сделано лишнего, но без этого невозможно было получить опыт. А опыт, полученный на ошибках - самый лучший. Но проблема оказалась не столько в разборе стрелы, сколько в РВД, которые были внутри нее. Когда мы сняли шланги, встал вопрос, чтобы изготовить новые. Уже по виду было понятно, что это необычные рукава, а фитинги вообще были с дюймовой резьбой. Поездив по городу по изготовителям РВД стало понятно, что ничего мы тут не найдем. Мало того, что на нас смотрели как на сумашедших, так еще поступали бредовые предложения об изготовлении всевозможных переходников с дюймовой резьбы на отечественную метрическую. Благо тогда хватило ума не поддаваться на эти бредни и не останавливать поиски. Естественно в своем городе мы ничего не нашли. Одна единственная японская автовышка на весь город - информации и специалистов никаких небыло. Благо столица была недалеко - на нее и оставалась вся надежда.
Посетив в столице специализированный центр по изготовлению рукавов высокого давления, мы получили информацию, что такие рукава можно изготовить по образцам, и проблем с дюймовой резьбой и фитингами небыло. Воодушевившись надеждой на светлое будущее, мы взяли в охапку наши старые шланги, запаслись большой суммой денег и отправились в столицу делать новые рукава высокого давления по нашим образцам. Процесс изготовления занял несколько часов. В конечном итоге мы получили новые рукава из морозостойкой резины с одинарным металлическим армированием. При этом наружные диаметры рукавов были незначительно больше оригинала. По словам мастера, это небыло проблемой, типа 1 мм роли не играет. А ключевое слово "морозостойкая" вообще внушало большие перспективы на будущее. Как хвалился мастер, который изготавливал рукава: "В Японии таких морозов, как у нас, не бывает", так что эти рукава должны были служить вечно. Но на тот момент мы вообще не понимали ничего и верили всякому бреду, главное, что проблема была решена.
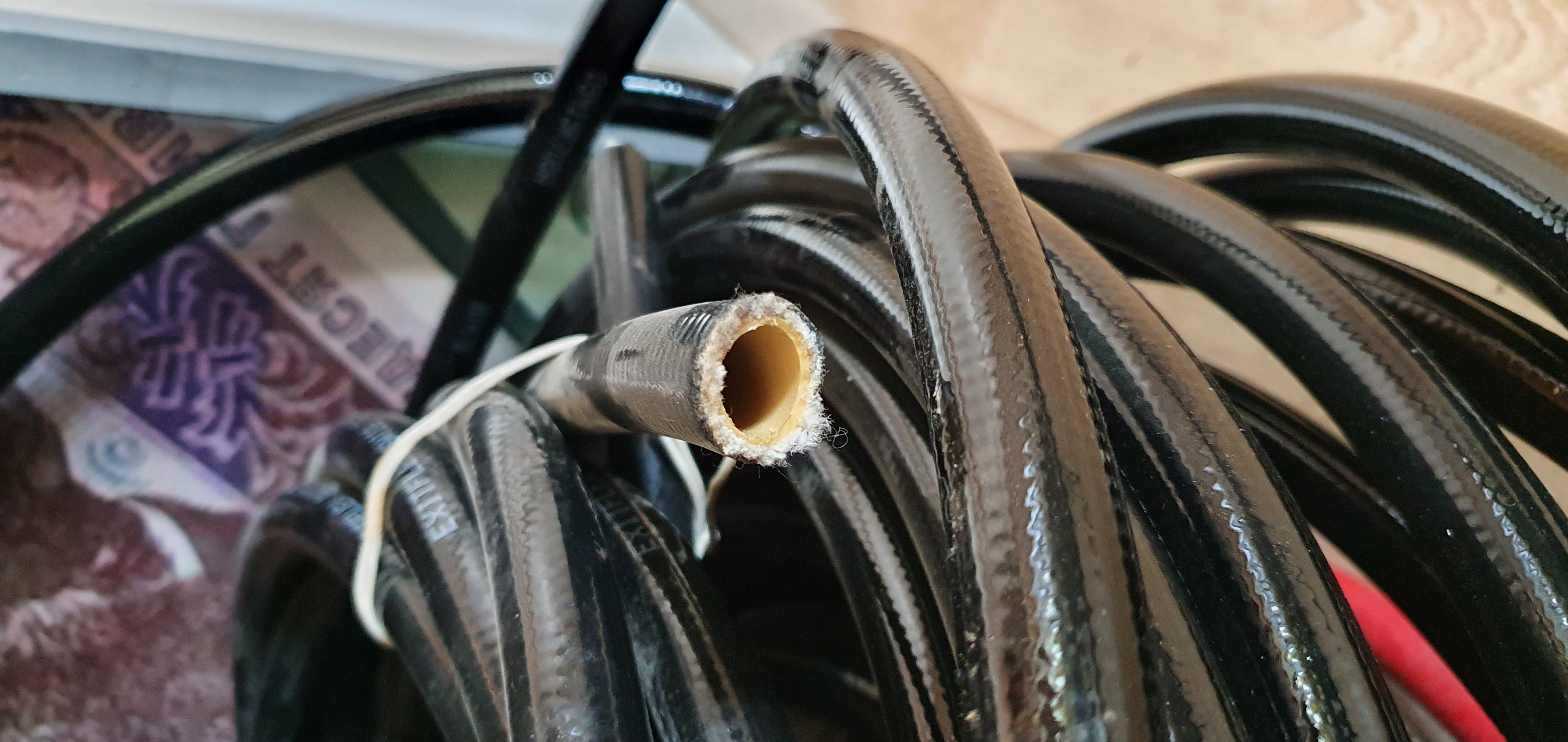
Новые рукава устанавливали еще неделю. Сначала не могли понять, какой рукав куда идет, потом переделывали натяжные троса, под них вытачивали новые натяжители с резьбой. Все это запасовали на ролики. Потом на роликах меняли подшипники, вычищали из стрелы грязь и ветки. Какие-то пальцы вытачивали, совещались про натяжку шлангов и т.п. - в общем неделя рабочего процесса. После установки и сборки вздохнули - гидравлика заработала. Стрела выдвигалась и задвигалась. Это была победа. Мы, парни из русской глубинки, встали в один ряд с инженерами из Японии, смогли починить ихнюю технику своими собственными руками. Эйфория одним словом.
Правда радость оказалась недолгой. Не прошло и месяца как шланги внутри стрелы потекли снова. Разбирая стрелу мы не могли понять, что же сделали не так. На этот раз разборка заняла уже два дня. Опыт уже был. Схема отработана. После разборки мы увидели следующую картину: шланги были все как-будто порезаны, проволока от металлического армирования торчала то тут то там. Создавалось впечатление, что шлангам не месяц, а несколько лет. На ум приходило несколько ошибок, которые мы могли допустить: неверная натяжка, попадание посторонних предметов внутрь стрелы, несоответствие посадочного места на ролике диаметру шланга, низкое качество шлангов. Но все предположения оказались неверными. Мы стали обзванивать другие фирмы в столице, чтобы собрать хоть какую-то информацию. И в одном представительстве чешкой фирмы, которая продавала различные шланги для производств, нам открыли в прямом смысле этого слова "новый мир" касательно наших рукавов высокого давления. Там пояснили, что уже сталкивались с такой проблемой и не раз ее решали. Предложили приехать к ним с образцами старых и новых рукавов, что мы незамедлительно и сделали. Приехав на эту фирму, мы ни разу не пожалели, люди в доступной форме, используя подручный инструмент показали нам что происходит с нашими рукавами и с теми, что мы заказали в другом месте, при движении по роликам, какие напряжения происходят внутри и почему у нас возникла проблема. Показали технические характеристики наших и "новых" рукавов. Оказалось, что сделанные рукава не соответствуют параметрам роликов, они не могут гнуться по такому маленькому диаметру, а металлическое армирование вообще не имеет гибкости и при движении по роликам просто рвет защитную оболочку и вылезает наружу. Более того наши рукава имели снаружи стойкое к истиранию покрытие, которое предназначено именно для движения по роликам и не стирается даже спустя продолжительное время. Разрезав наш шланг, они показали, что внутри имеется полимерная трубка, которая непосредственно держит давление и очень хорошо гнется, а армирует трубку синтетическое тканевое волокно, которое также имеет значительную гибкость без деформации. Выводом стало то, что резиновые рукава, даже с температуростойкой резиной, и уж тем более с металлическим армированием никак не подходят в нашем случае. После такой лекции пришлось идти за литром водки и закуской, чтобы как-то отблагодарить ребят из этой фирмы. Полученная информация на тот момент был очень ценной.
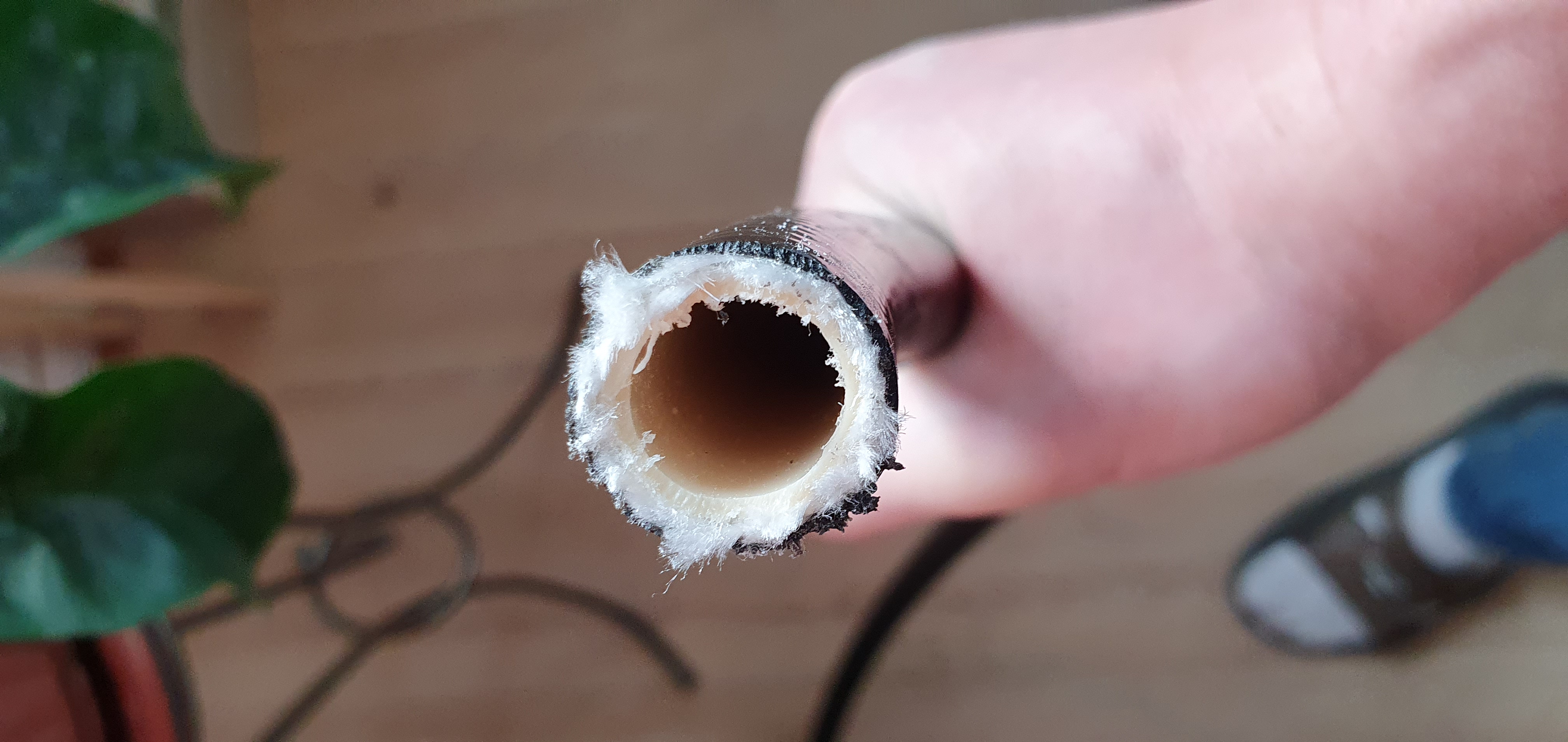
После небольшого перерыва удалось получить дополнительную информацию о том, что у них есть в продаже такие рукава и даже могут сделать опрессовку. Однако возникла проблема в том, что нет фитингов с дюймовой резьбой, поскольку такие не применяются в Европе. Однако осмотрев шланги, которые нам сделали в другой фирме, было предложено попробовать срезать с них фитинги и опрессовать заново. Все-таки литр водки и хорошая закуска наверно сыграли свою роль, а может ребята просто над нами сжалились, потому что в попытках решения этого вопроса дело уже доходило до слез. После просчета стоимости услуг и материала мы начали подбивать свои финансы, ценник оказался значительно дороже, чем отечественные шланги, но выхода уже небыло, цель была совсем близко. Денег немного не хватало, но нам сделали скидку на перспективу, что тоже было немаловажным фактором. В общем все эти разговоры, лекции и сама работа заняли почти полный рабочий день. Мы постарались помочь, чем смогли. Где-то поддержать, где-то отрезать болгаркой, что-то отмерить, в общем включились тоже в работу. Ну и скидку надо было как-то отрабатывать. По итогам дня мы получили в собственность термопластиковые рукава для нашей автовышки, при этом они были чешского (импортного) производства. Также получили рекомендации по натяжке и эксплуатации. Ну и вообще, все заданные вопросы имели ответ, что очень порадовало. Общение вышло очень продуктивным и душевным. А информация о том, что через несколько дней шланги надо будет подтянуть, поскольку они немного растянутся после того как были намотаны на бобину, вообще осталась с нами как должная аксиома, которой мы пользуемся и по сей день.
В результате данные шланги были установлены нами на автовышку. Через неделю была проведена их подтяжка. Отслужили они нам верой и правдой почти 7 лет - вот что значит качество. А встреча с этими ребятами для меня осталась в памяти до сих пор. Может времена тогда такие были, может люди просто отзывчивые попались. Сейчас уже все реже встречаешь такое, люди стали другими, за копейку "давятся", чего уж говорить про отношение, если не "послали" и то хорошо. Рукава такие, слава прогрессу, появились, по крайней мере в больших городах, в свободной продаже. Ну а мы, чтобы не рисковать и не тратить время на их поиски, купили обжимное оборудование, завезли эти рукава к себе на склад. Отработали технологию и теперь можем предложить услуги по изготовлению РВД на японские автовышки. Получается вроде неплохо, есть клиенты даже из ближнего зарубежья. Многие машины ходят уже больше 5 лет. Ну и ремонт той первой автовышки перерос у нас в полноценный сервис по гидравлике. Разбираем стрелы теперь за день, перебираем гидроцилиндры, переделываем насосы - на своих машинах научились...
© Дядя Fedor, февраль 2021 г.
При перепечатке материала прямая ссылка на сайт www.podnimai.ru обязательна!
Смотрите видео про экскаватор-погрузчик на моем канале в Яндекс.Дзене
Читайте еще статьи на нашем сайте:
- про японскую автовышку
- про автокраны
« К статьям