Изготовление нового штока для гидроцилиндра
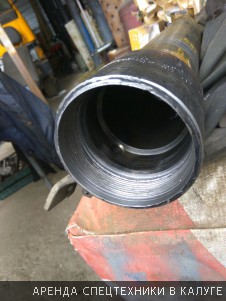
При работе автовышки на спиливании деревьев произошел небольшой казус: надпиленная ветка лопнула и со всей силой ударила по штоку гидроцилиндра подъема дополнительного колена. В результате удара шток получил повреждения: деформацию на всей длине, сколы зеркальной поверхности общей площадью более одного квадратного сантиметра, при складывании колена появились значительные подтеки гидравлического масла. По итогам обследования было принято решение о его замене, т.к. последствия удара были невосстановимыми. Для замены штока необходимо было разобрать гидроцилиндр. Ввиду того, что его не разбирали за все время эксплуатации автовышки, то сразу возникли сложности. Гайка никак не откручивалась. В рзультате были применены способы откручивания, в результате которых резьба и внутренние уплотнения были повреждены. При разборке применялось нагревание гидроцилиндра, а также он был зажат в токарный станок для создания большого усилия, чтобы свернуть гайку. После разборки стало понятно, что гидроцилиндр фатально поврежден и требует замены. Однако поискав варианты замены стало понятно, что по цене и времени альтернативы, кроме как восстанавливать старый, нет. Для сравнения, новый из Японии стоил 300 тысяч рублей, изготовление в специализированных организациях по чертежам или образцу - 120 тысяч, при этом нет никаких гарантий качества и материалы изготовления довольно спорны.
Поврежденная часть гидроцилиндра с резьбой была срезана, сам стакан с хромированной поверхностью пошел как основа, была изготовлена новая гайка в соответствии с точными размерами старой, а также была изготовлена новая ответная часть гайки вместо поврежденной. Затем в ней была нарезана резьба и она соединилась с основной частью цилиндра с помощью газовой сварки. Был изготовлен новый шток из специализированной стали, по точным размерам, снятым со старого. Шток был подвергнут цементации и шлифованию для увеличения прочности и придания зеркальной поверхности. Затем необходимо было подобрать уплотнения (манжеты). Поскольку старые были необратимы повреждены, то подбор происходил по замеру соответствующих деталей. Как обычно, в магазинах резино-технических изделий Калуги, ничего найти не удалось. Поэтому, после снятия соответствующих размеров были направлены запросы в специализированные магазины в регионах России. В тот же день были подобраны необходимые уплотнения, оплачены и высланы.
После сборки гидроцилиндра, он был обработан антикоррозионной краской, чтобы места сварки не подвергались коррозии. Затем гидроцилиндр был установлен на автовышку. После пуска масла в системе, необходимо удалить воздух из гидроцилиндра при помощи соответствующего штуцера. Затем плавно необходимо проверить его работоспособность. В случае отсутствия подтеков гидравлического масла и полной работоспособности, можно переходить к следующему этапу проверки.
И вот пришло время провести испытание гидроцилиндра. Номинальная грузоподъемность японской автовышки модели AT-185TG составляет 200 кг. Испытания проводят нагрузкой, превышающей номинальную грузоподъемность на 50%. В случае успешного завершения испытания, автовышка считается годной к эксплуатации, о чем делается соответствующая запись в паспорте. После завершения всех формальностей и получения допуска на ввод в эксплуатацию после ремонта, можно приступать к непосредственной эксплуатации автовышки.
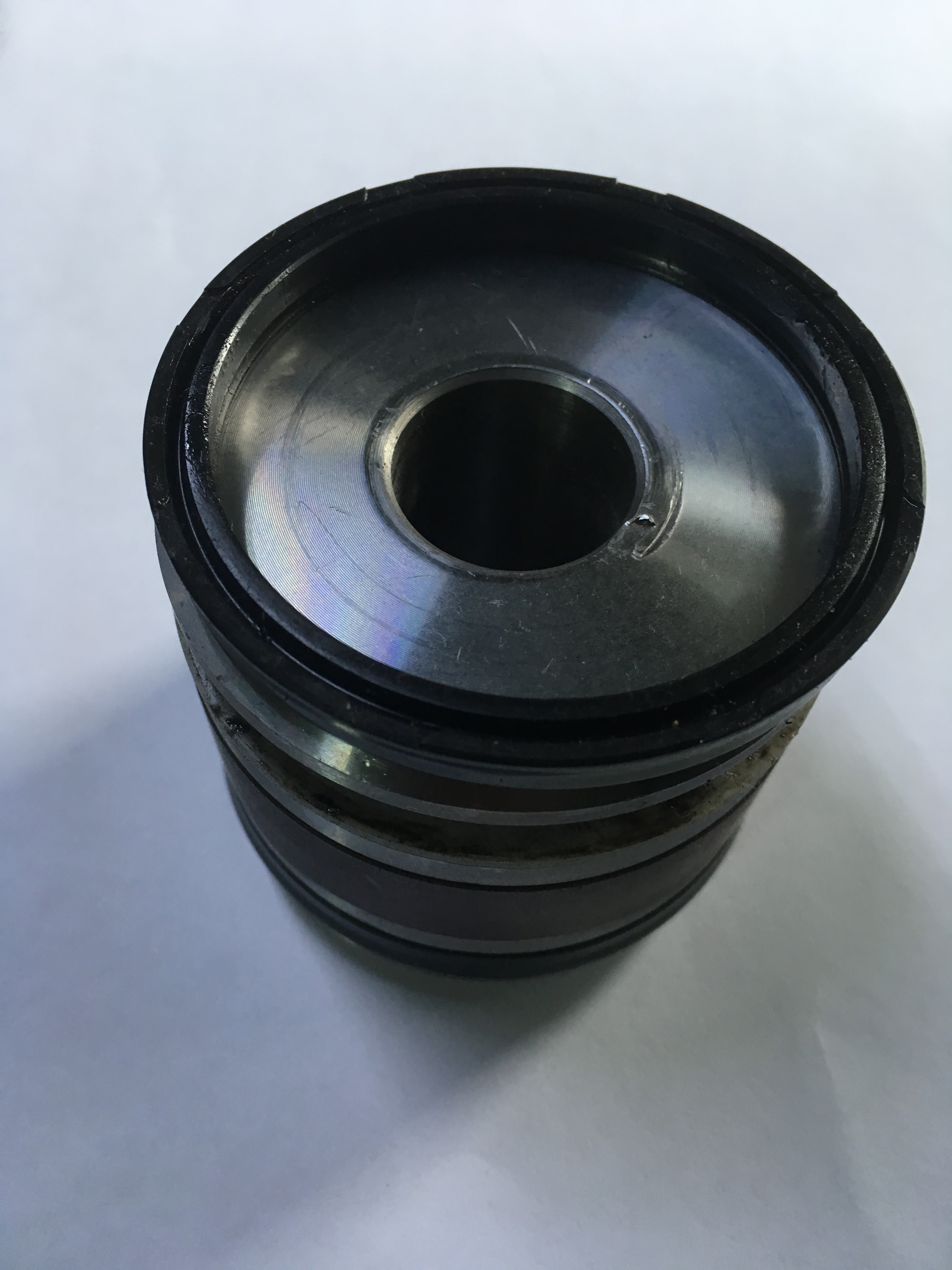
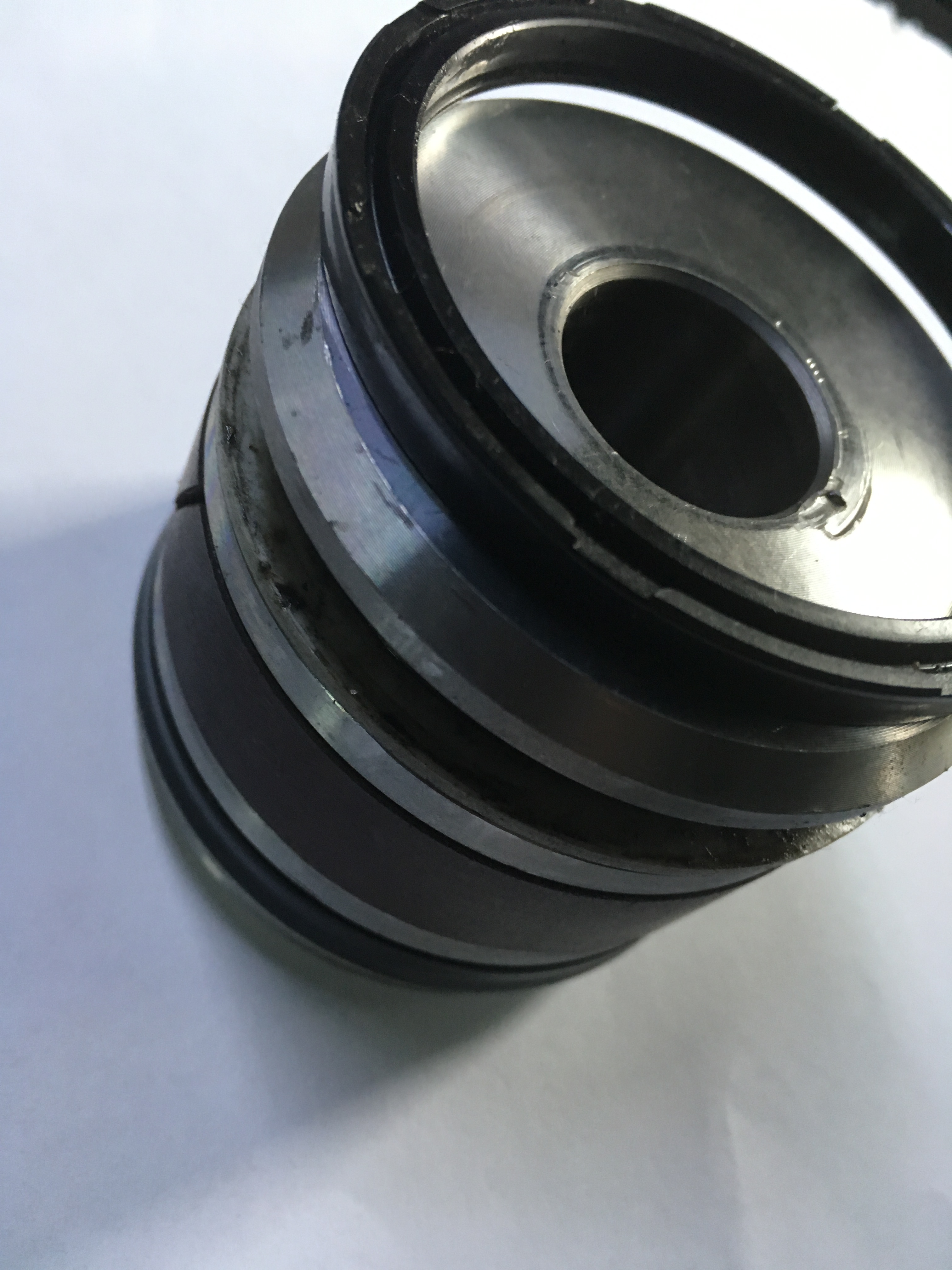
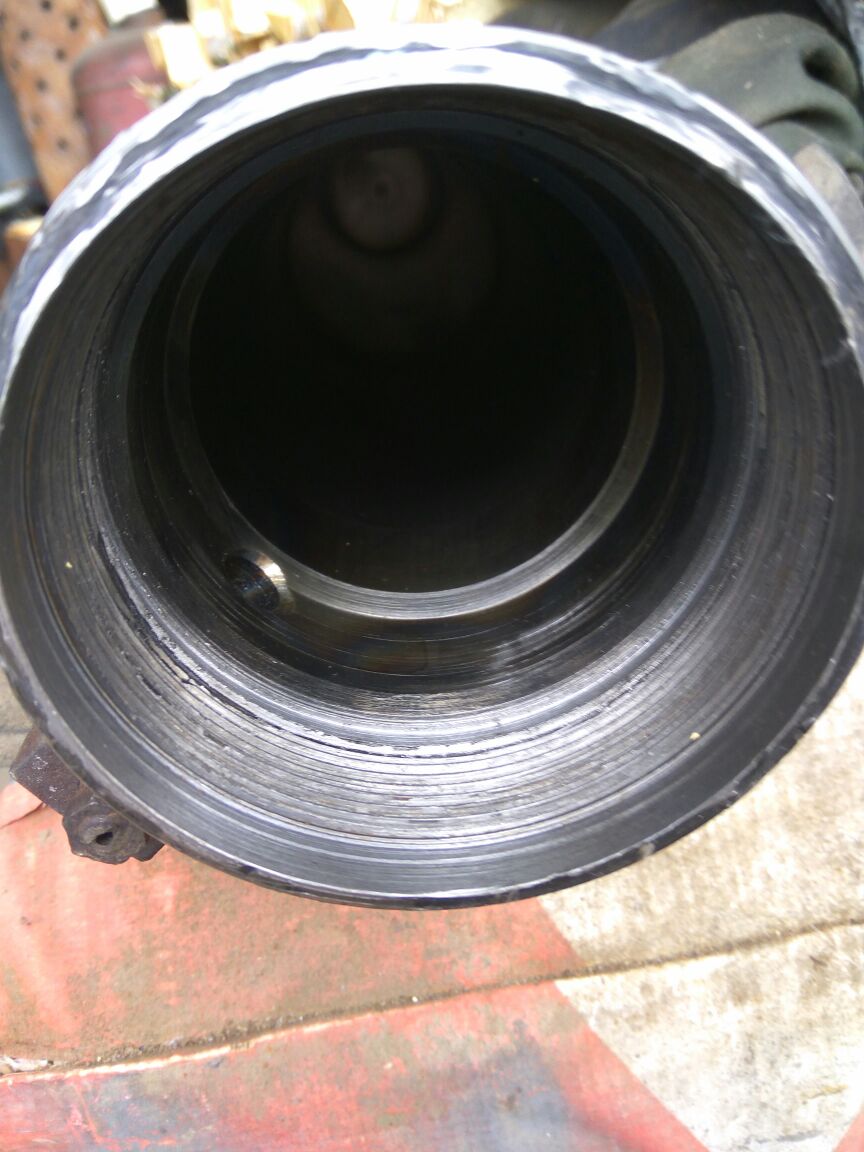
Работы проведены в автосервисе "Дядя Федор" в период с 10 августа 2016 г. по 30 сентября 2016 г. Наши контактные данные находятся в соответствующем разделе этого сайта.
Поврежденная часть гидроцилиндра с резьбой была срезана, сам стакан с хромированной поверхностью пошел как основа, была изготовлена новая гайка в соответствии с точными размерами старой, а также была изготовлена новая ответная часть гайки вместо поврежденной. Затем в ней была нарезана резьба и она соединилась с основной частью цилиндра с помощью газовой сварки. Был изготовлен новый шток из специализированной стали, по точным размерам, снятым со старого. Шток был подвергнут цементации и шлифованию для увеличения прочности и придания зеркальной поверхности. Затем необходимо было подобрать уплотнения (манжеты). Поскольку старые были необратимы повреждены, то подбор происходил по замеру соответствующих деталей. Как обычно, в магазинах резино-технических изделий Калуги, ничего найти не удалось. Поэтому, после снятия соответствующих размеров были направлены запросы в специализированные магазины в регионах России. В тот же день были подобраны необходимые уплотнения, оплачены и высланы.
После сборки гидроцилиндра, он был обработан антикоррозионной краской, чтобы места сварки не подвергались коррозии. Затем гидроцилиндр был установлен на автовышку. После пуска масла в системе, необходимо удалить воздух из гидроцилиндра при помощи соответствующего штуцера. Затем плавно необходимо проверить его работоспособность. В случае отсутствия подтеков гидравлического масла и полной работоспособности, можно переходить к следующему этапу проверки.
И вот пришло время провести испытание гидроцилиндра. Номинальная грузоподъемность японской автовышки модели AT-185TG составляет 200 кг. Испытания проводят нагрузкой, превышающей номинальную грузоподъемность на 50%. В случае успешного завершения испытания, автовышка считается годной к эксплуатации, о чем делается соответствующая запись в паспорте. После завершения всех формальностей и получения допуска на ввод в эксплуатацию после ремонта, можно приступать к непосредственной эксплуатации автовышки.
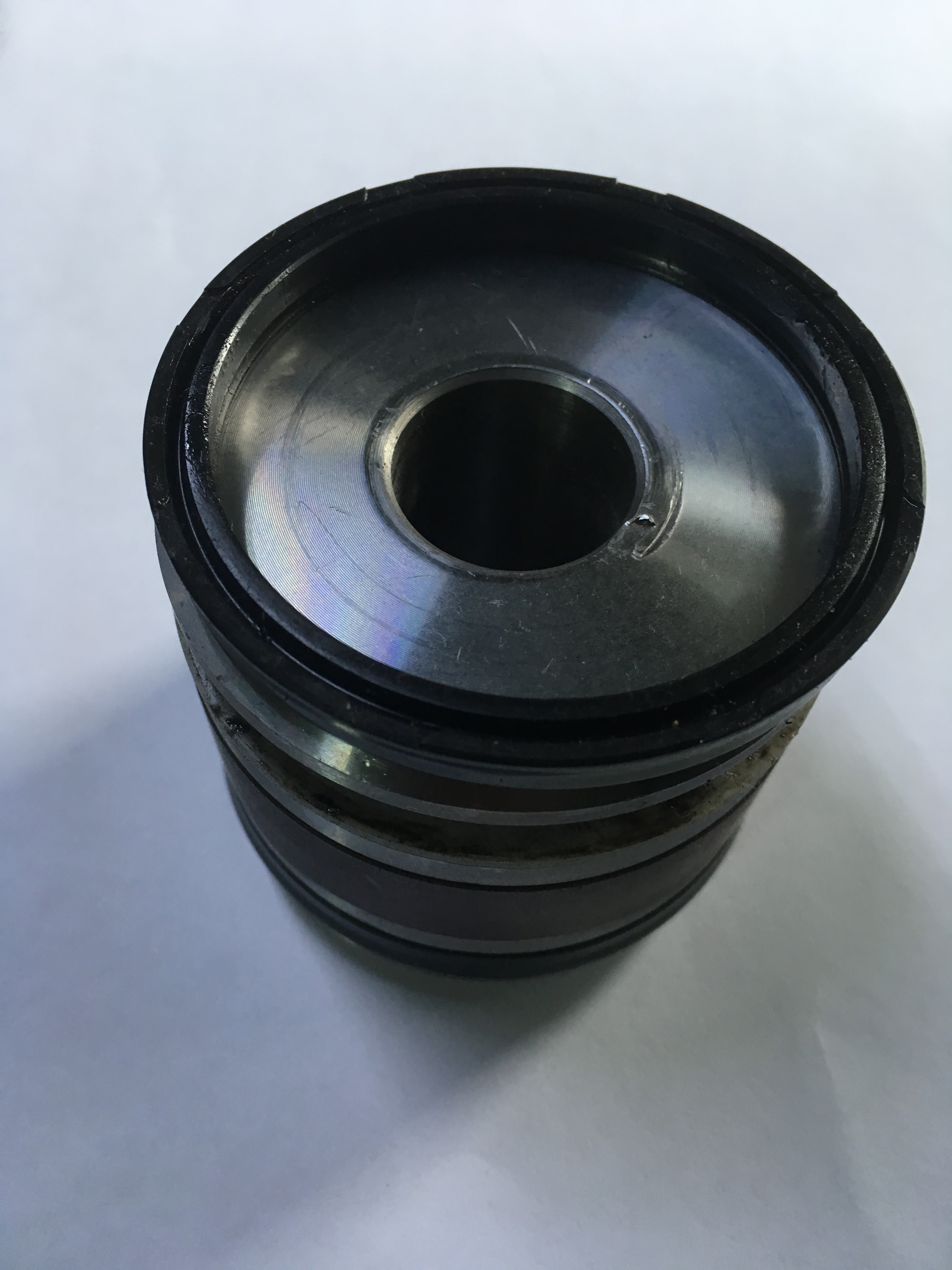
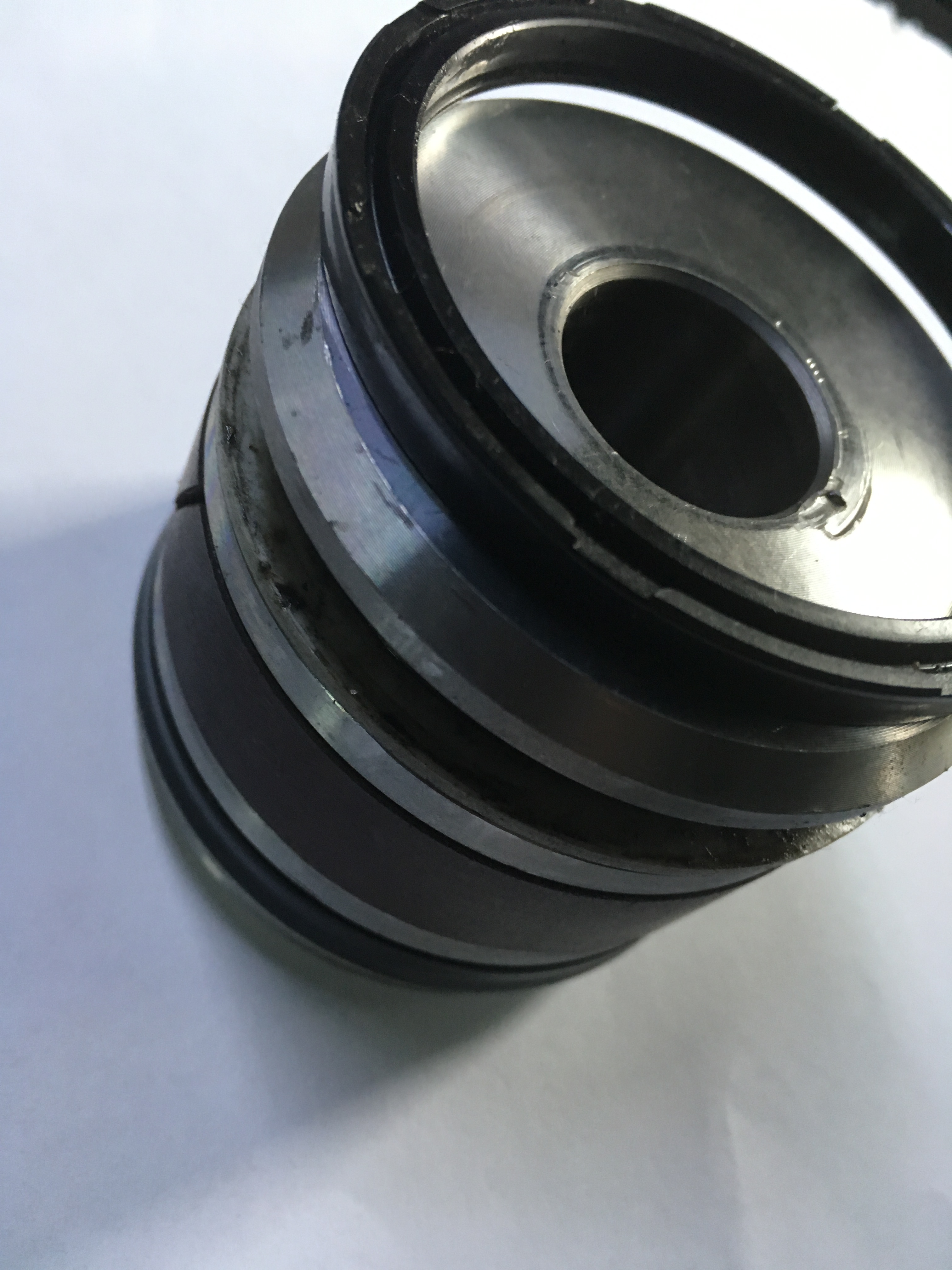
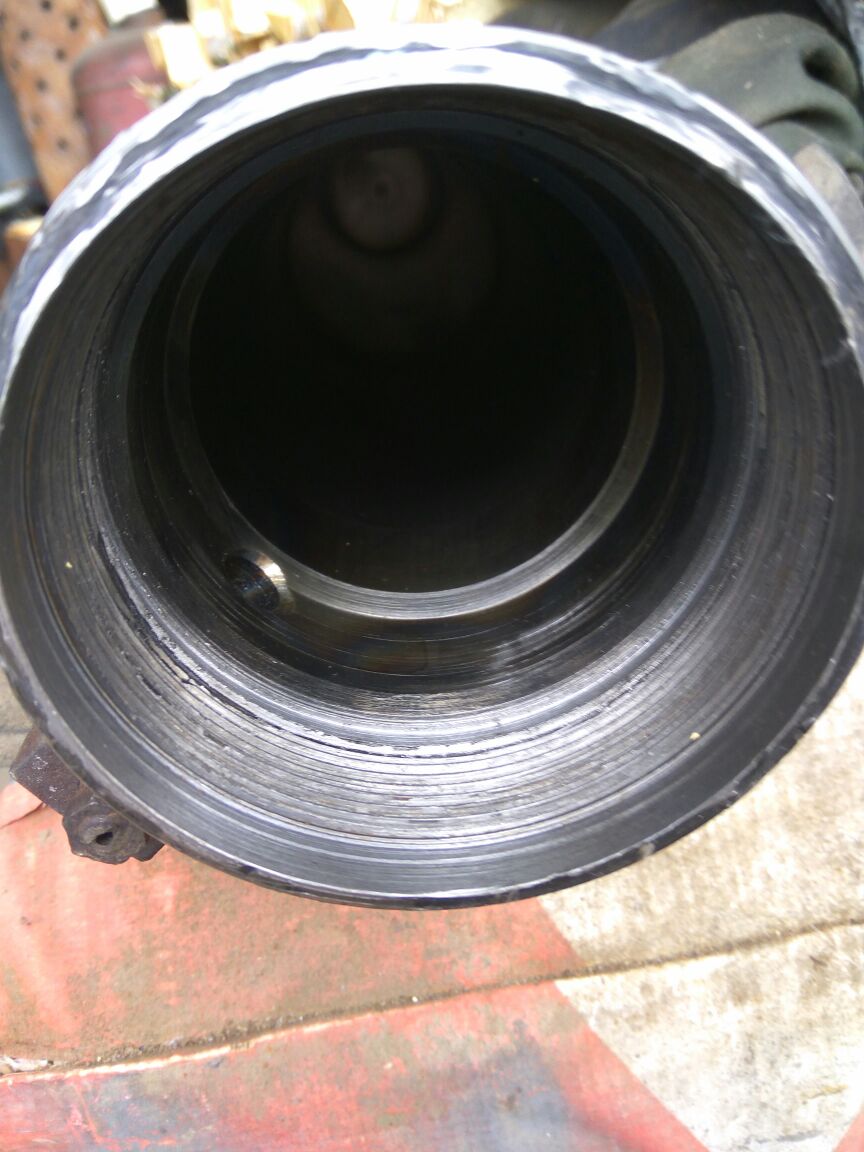
Работы проведены в автосервисе "Дядя Федор" в период с 10 августа 2016 г. по 30 сентября 2016 г. Наши контактные данные находятся в соответствующем разделе этого сайта.